Optimizing overall equipment effectiveness at allnex

Full transparancy on production process

The Plan Board is a game changer

Digital Batch Cards for data collection
allnex is the global leader in Industrial Coating Resins with applications in automotive, packaging, industrial wood and more. allnex has 34 manufacturing facilities in Europe, Americas and Asia Pacific, serving customers in over 100 countries worldwide.
The challenge
One of the main challenges allnex is facing within operations is optimizing the overall equipment effectiveness (OEE). This means making more product in the same timeframe and optimizing the utilization. At the moment a lot of knowledge is in people’s heads and the production process is described and documented mainly on paper. So, improving efficiency and transparency is required by making data digitally available.
The solution
To improve the production and planning process, allnex chose Valtimo. A pilot project at the Wiesbaden site was started. Valtimo is used by the production teams to do the fine scheduling of SAP process orders and to create and execute digital batch cards for the production process.
Plan board: With the digital Plan board in Valtimo, the production team can do the fine scheduling of orders they receive from SAP. Each order is divided into process blocks that split up the production process into main steps and multiple user tasks. Based on the actual situation of the batch process the production team can define the exact starting points of each order and manage interdependencies with other blocks. The Plan board shows where each order stands at any specific moment. Color indications help the production team to see if a process block of an order is open, in progress, or done. It also shows if a process block goes too quick or too slow so adjustments can be made. The Plan Board is developed in cooperation with OptaZEN.
Batch cards: The batch card is the step-by-step description of a specific production process. It guides the operators through all necessary activities. For example, when to add certain raw materials, when and how temperature or pressure should be adjusted, and how to act when certain deviations occur. Batch cards further allow for documentation of the completion of these activities and protocolling of details, but also summarize the gathered data on different focus areas like raw materials, samples, process block durations etc. Besides integration with SAP (IT) also an integration with the operational technology (OT) is in place so not all data has to be entered manually. This allows, for example, to prefill protocols with temperature and pressure values that are captured via sensors or with raw material amounts that are captured via flow meters.
The batch card used to be a paper-based system with sometimes over 50 pages. With the introduction of the Valtimo Batch Card Configurator this is now fully digitalized. With the Batch Card Configurator the production team can now create a complete production process with all the required checks and protocols by using a drag and drop interface. Existing batch cards can be re-used and adjusted to assure quality. Furthermore, the collected data from the Plan board and the Batch Cards can be used for data analysis to optimize the processes.
The result
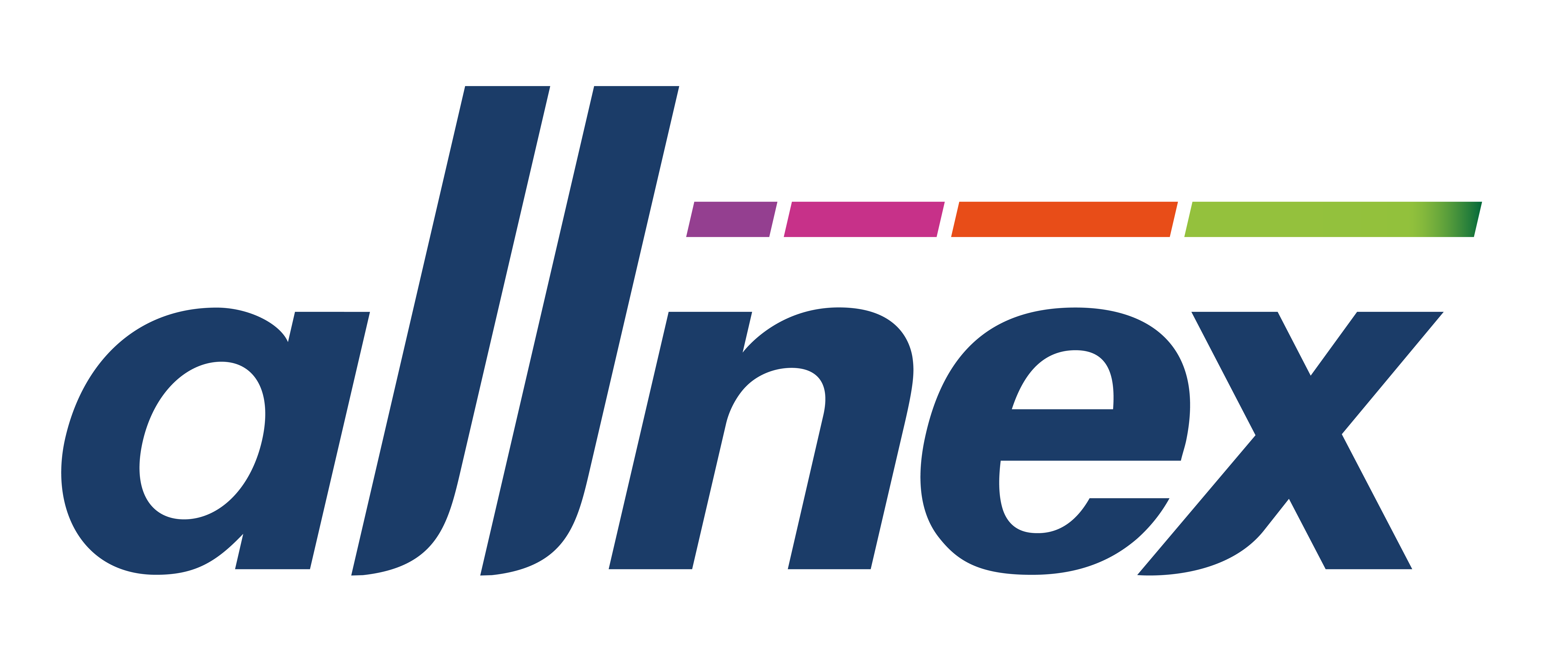
We want to make more product within the same timeframe with the given assets that we have. To reach that we need to have all the data digital.
Sophie Zellmer, Global Implementation Manager for Digital Operations